The Top Materials for CNC Milling: Pros and Cons

CNC milling has turned the tide towards modernizing manufacturing in several industries, revolutionizing and creating opportunities for creating more precise and intricate design work. Applications range from the aerospace industry to consumer products, and the list keeps growing. Of course, selecting the right material for CNC milling is critical.
However, the right choice affects the quality of your projects, savings, and working efficiency. Therefore, you will consider the best materials for CNC milling herein, analyzing the pros and cons of each one to help you make informed decisions.
What is CNC Milling?
CNC milling is a manufacturing process involving rotating tools that remove material from a workpiece. The workpiece is firmly clamped to a milling table that can rotate along various planes. In so doing, the tool can operate from multiple angles. Advanced CNC milling machines may even incorporate five or more independent motion axes, thus permitting them to craft intricate shapes without moving the workpiece onto another machine.
Advanced CNC materials selection thus greatly affects precision, durability, and surface quality. A wrong selection might lead to either structural weakness or higher costs, with negative effects on aesthetics; hence, knowing the properties and limits of the materials is very important.
Aluminum
Aluminum has become very popular in CNC milling. It offers a good mix of strength, lightness, and versatility. Typical alloys among CNC milling components are 6061 and 7075 aluminum. They prove their different qualities for different applications. Aluminum's ability to be machined easily while maintaining structural integrity has always endeared it to engineers and hobbyists.
Pros
- Lightweight But Strong: A high strength-to-weight ratio makes aluminum suitable for application areas where weight reduction is necessary without strength loss.
- Excellent Machinability: It can be easily machined in CNC machines, permitting high accuracy and smooth surface finishes.
- Very Good Thermal and Electrical Conductivity: Aluminum rapidly dissipates heat and carries electricity, thus advantageous for electronic housing and heatsinks.
Cons
- Higher cost: While CNC milling services cost more regarding other materials, such as wood or some plastics, for using aluminum, the costs might be higher, meaning increased project costs.
- Difficult to weld: Welding aluminum requires sophisticated techniques and equipment, which causes complications in fabrication.
Wood
Wood has maintained its status as a raw material for craftsmanship for thousands of years. CNC milling has thrown modern dimensions of precision into traditional woodwork. Hardwoods such as maple, oak, walnut, and softwoods like pine and cedar are most commonly found to be CNC materials owing to their peculiar textures and properties.
Pros
- Wood's Natural Grain: The texture of natural grain and colors establishes aesthetic qualities in furniture and decoration products.
- Easy to Work: Wood is usually cut, shaped, and carved easily, allowing for intricate designs and detailed work with CNC machines.
- Cost-Effective: Relatively cheap and widespread compared to metals or some plastics, wood is another panacea for many projects.
Cons
- Sensitive to Moisture and Temperature Effects: Wood may warp, swell, or shrink, depending on changing humidity and temperature, affecting the stability of the finished product.
- Produces Fine Dust: CNC material wood generates fine dust, a problem that must be solved with good ventilation and appropriate safety personal protective equipment.
Acrylic
Acrylic or PMMA is the common name for a transparent thermoplastic, which is lightweight and unbreakable, like glass. Two types of acrylic, cast and extruded, are characterized by their different properties in CNC milling applications.
Pros
- Appearance: Acrylic is easy to view perceptively and has a very glass-like appearance, making it perfect for applications where glass does not want to be so heavy or fragile.
- Lightweight and easy to work with: Compared to glass, acrylic is much lighter and easily machined, making way for a more intricate design and detailed cuts.
- Excellent Dimensional Stability: Acrylic can withstand various conditions and be manipulative without structural modification, establishing considerable consistency of quality in the end product.
- UV and Weather Resistant: Especially for cast acrylic, this type of acrylic will resist both the UV rays and its weathering effects, making it excellent for use outdoors.
Cons
- Harm most likely to crack or chip: They are brittle and tend to crack or chip when machined or handled if not treated precisely and properly.
- Machining creates heat: Overheating can cause the acrylic to melt or warp, requiring precision control of milling parameters in CNC.
- More Expensive than Some Plastics: Cheaper than glass but more expensive than other plastics like PVC or polycarbonate.
CNC Milling 3D Printing Materials: PLA and ABS
PLA (Polylactic Acid) and ABS (Acrylonitrile Butadiene Styrene) are common raw materials in 3D printing. These thermoplastics have peculiar qualities, and each serves particular applications but has merits and demerits.
PLA (Polylactic Acid)
Pros
- Environment-Friendly: Biodegradable- Renewable raw material sources like corn starch PLA are considered green compared to their petroleum-derived plastics.
- Easy to Machine: Machining PLA results in nearer-to-true parts requiring no high-temperature processing and allows smooth, fine cuts.
- Smooth Surface Finish: Fine surface finish would be a self-developed quality of PLA that needs less effort post-processing.
Cons
- Lower Heat Resistant: Deformation of PLA occurs at relatively low temperatures; therefore, this plastic cannot be used for applications exposing it to heat.
- Brittle Compared to ABS: Under stress, PLA cracks and breaks up more easily and could not be recommended for heavy-duty or high-impact applications.
- Low Strength: Because its mechanical strength is lower than ABS, PLA is limited to functional parts in terms of life expectancy.
ABS (Acrylonitrile Butadiene Styrene)
Pros
- Impact Resistant and Strengthier: ABS provides very high working mechanical strength and impact resistance compared to PLA, which justifies its use in functional parts.
- Better Heat Resistance: It resists deformation at higher temperatures and has a quality that makes it useful for heat environments.
- Eases in Post-Processing and Painting: ABS's surface smoothens and can easily be sanded or painted with finishing flexibilities.
Cons
- Fumes Generate During Machining: Fumes while machining from ABS require good ventilation and safety measures to protect users.
- Prone to Warping and Shrinkage: ABS can warp or shrink while cooling, requiring special handling and controlled machining environments.
Conclusion
The materials you use for CNC milling depend on the project in question. Aluminum provides a special balance of strength and machine versatility, while steel guarantees the best durability of most materials. Of course, there is a wood aesthetic. One can also think of acrylics from the standpoint of clear and transparent plastics such as PLA, ABS, and even titanium, which provide the platform for high-strength pure materials with corrosion resistance. By differentiating the various benefits and drawbacks of each material, it ensures the best quality, cost-efficiency, and performance for your projects.
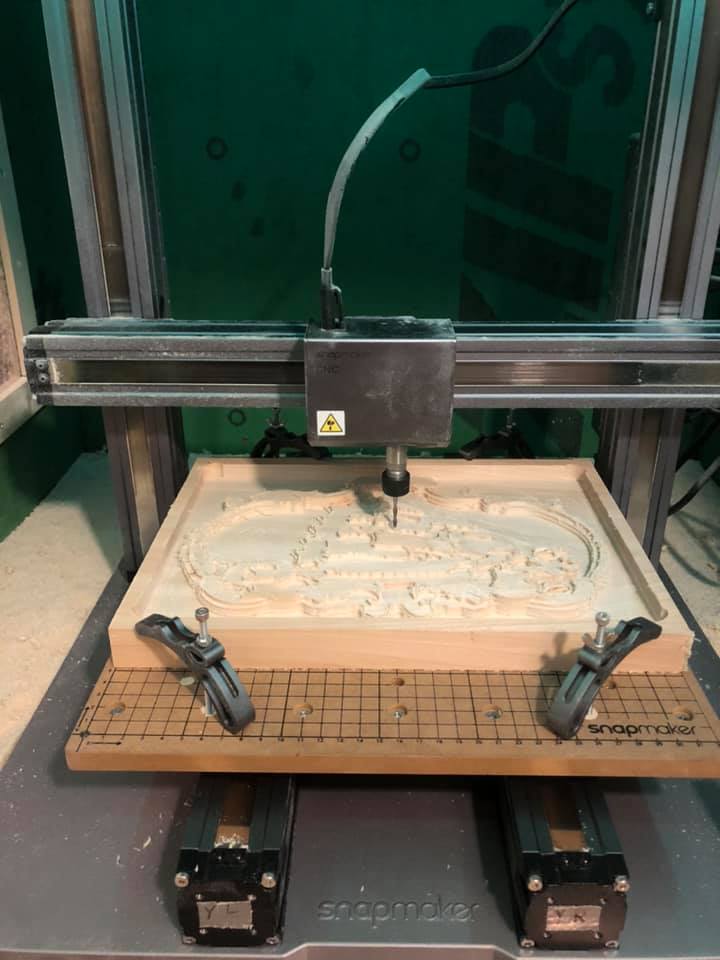
Snapmaker’s CNC modules are a perfect means of realizing your designs for advanced CNC milling. Whether precision or versatility is needed, Snapmaker has quality tools to improve your craftsmanship. They're designed to handle a wide range of materials, ensuring precision and versatility for your projects:
Supported Materials (Ideal)
- Hardwoods: Beech, Walnut
- Softwoods, HDF, MDF, Plywood
- Jade, Carbon Fiber, Acrylic
- Epoxy Tooling Board, PCB
These materials are perfect for intricate detailing, durable finishes, and high-quality results in furniture making, prototypes, and electronic components.
Supported Materials (Capable)
- Aluminum (1000-6000 Series)
- Brass
- Red Copper
While capable of machining these metals, achieving the best results may require specialized tooling and optimized settings. Click here for more detailed information about the supported materials for Snapmaker’s CNC modules.
Ready to elevate your craftsmanship? Explore Snapmaker’s CNC solutions to bring your creative visions to life with unmatched precision and flexibility.