Introducing Snapmaker J1 3D Printer: IDEX Made Faster
J1 features lightning-fast IDEX, which brings you prints of high resolution while increasing the printing speed to 350 mm/s.
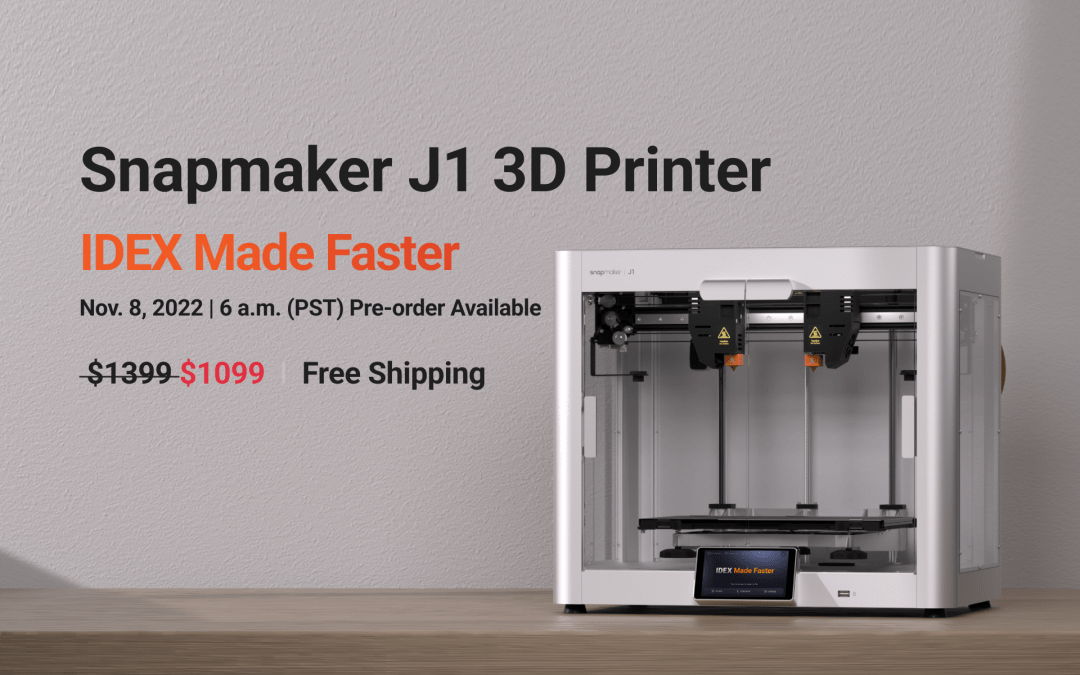
Hi makers,
In the previous article, we announced the return of Snapmaker's early founding team members with their J1 IDEX 3D printer. Today, we will further unveil many more exciting features of J1, which bring infinite possibilities and make 3D printing a simple joy!

Up to 350 mm/s printing speed and up to 10000 mm/s² acceleration
J1 brings you prints of high resolution while increasing the printing speed to 350 mm/s. It is made possible by the optimization of the vibration compensation technology. This technology reduces the vibrations caused by high-speed movements, minimizing ringing to enhance print quality. With the maximum acceleration of 10000 mm/s², you can realize small models packed with details with efficiency. Overall, the usual printing time is reduced by ⅔ while impeccable details are still within reach. [1]
https://videopress.com/v/RP5ERbTJ?resizeToParent=true&cover=true&preloadContent=metadata&useAverageColor=true
IDEXcel in dual-material printing
Compared with a multi-material unit on a single extruder, IDEX dual-material printing requires less time in filament changing and creates less waste. Plus, IDEX offers the cleanest two-extruder solution that prevents cross-contamination. It creates a clean interface between two materials, embracing hassle-free removal and avoiding stains and weird blending along the seam.
Breakaway supports & dissolvable supports for effortless removal and accurate details
Building and removing support can look like rocket science sometimes, but we've done the math for you–steady support, clean interface, effortless removal, and minimal post-processing needed to maintain high dimensional accuracy.

Breakaway filament offers the same support as normal materials but is much easier to remove without the need for further post-processing. J1 supports PVA and other dissolvable materials. Soak the print, and the supports dissolve, leading to a smooth surface and excellent dimensional accuracy. If you are looking for complex geometry, hollow structures, and exquisite details, this is for you.
Choose different settings for two extruders to maximize the performance of individual filaments. For example, you can combine the strength of nylon with the flexibility of TPU for functional parts that can stand daily wear and tear impressively. Or, you can produce bicolor prints and add a splash of personality to your concept models, miniatures, party essentials, gift items, and home decor. Even more, you can have different materials on the walls and the infill. By printing infill with economical materials plus a large-diameter nozzle, you can now spend most of your time and money budget on working the exterior to perfection.
Copy Mode & Mirror Mode double your productivity
IDEX is the only extrusion system with two separate extruders moving independently on the X-axis, enabling you to run two prints simultaneously. With Copy Mode and Mirror Mode, you can halve your wait time and double your productivity. Copy Mode is especially suitable for batch printing, empowering studios and enthusiasts. If one of the prints runs into an issue, you can stop that print without affecting the other. This mode is a lifesaver for a promised delivery on a tight schedule. Under Mirror Mode, J1 directly mirrors your model and prints the original and the mirrored one in one go. For a symmetrical model, you can import half of it and print it in Mirror Mode to cut your wait time by 50%, perfect for quick drafts and concept models. Like in the Copy Mode, you can stop one print without affecting the other.

Ultimate rigidity from the one-piece casted parts, high-precision linear rails, aluminum alloy frame
J1's body comprises an upper frame and a base made by one-piece die casting, and four aluminum alloy bars. Making the body with just a few highly integrated parts—an approach long adopted by the automotive industry—facilitates precision assembly. J1 is so rigid and reliable with minimal wobble and deformation possible that you can do a large-print marathon and get all the prints with uncompromising quality.
The industrial-grade linear rails are made by CNC grinding at the micron level, ensuring smooth and steady movements. A significant rise in precision, rigidity, and durability for you to savor a fast, accurate, and steady-making experience. The repeatability measures ± 0.03 mm (X/Y) and ± 0.02 mm (Z). [2] Expected Lifespan is over 10 Years.[3]
J1 inherits Snapmaker's iconic all-metal design which is highly valued by users for its rigidity and durability. It provides better heat dissipation with the main board and power supply spread out on the base and aluminum alloy as its main material.
Print with advanced materials like PA, PC, and TPU, and deliver fabulous results
Extruders are redesigned to deliver a superb performance consistently with demanding, advanced materials, including nylon, reinforced nylon, PC, TPU and PA-CF. First, 300°C All-metal Hot Ends enable you to print with high-temperature filaments, like nylon, reinforced nylon, PC and PA-CF. With silicone hot end socks preventing heat loss, filaments melting and heating up are much faster. Anti-clogging designs make the flow as smooth as possible.
Second, dual direct drives have excellent extrusion accuracy and are highly responsive, making deposition faster, smoother, and more accurately controlled. It is built in with a filament sensor to inform you and pause the print job in the case of filament runout, nozzle clogging, and other abnormalities that fail filament loading.
Third, the compact extrusion path of a unique design allows you to print seamlessly with TPU and many other flexible materials.
Fourth, the enclosed space provides stable ambient conditions to facilitate the consistently reliable performance of high-temperature materials. For instance, it keeps ABS and many other materials from warping.
4-minute intelligent calibration with no calibration card
We utilize electrical conduction to locate the two hot ends and the heated bed and measure the distances between the three entities—a creative solution to complex IDEX calibration. This time saver enables you to complete the calibration in 4 minutes under the Assist Mode. It reduces errors and arrives at better accuracy.
When the two hot ends touch the square opening on the heated bed, it sends out electronic signals to suggest their exact locations, and J1 calculates the offsets between them. J1 then auto-compensates the offsets during printing to ensure perfect XY alignment that avoids layer shifting and improves the success rate of dual-material prints.
A level print bed lays the foundation for successful 3D prints, but the bed leveling of IDEX printers can be very time-consuming. Using a PEI glass plate of high flatness, J1 can downsize from a 3 × 3 (9 points) or 4 × 4 (16 points) leveling to a 3-point one with no compromise on levelness and downtime dropped by 70–80%.[4] Turn the leveling wheel as guided on the touchscreen, and the bed is leveled for tip-top first-layer adhesion.
Using electrical conduction, J1 can calculate the distances between the hot ends and the heated bed. Thus, we were able to cut the step of moving the calibration card back and forth while adjusting the Z offset. Simply turn the thumb wheel as guided on the touchscreen and you are now the Z offset calibration guru!
In this article, we have shared lots of great things about this brand-new 3D printer of Snapmaker. We hope you have enjoyed it! We made every decision in the product development for one purpose–print better, better prints. Advancements in extruders, materials, structural designs, linear rails, and many other aspects are made for you to work to the fullest for every project.
From Oct 27 to Nov 17, we will recruit makers worldwide to review Snapmaker J1. You can enter to win the chance to try out and review J1 for free! Stay tuned.
[1] The data is estimated based on where regular IDEX 3D printers print at 50 mm/s to 80 mm/s and J1 prints at 350 mm/s for the same model. It may vary depending on the testing conditions and product iteration, and is for reference only.
[2] The data may vary depending on the testing conditions and product iteration, and is for reference only.
[3] The data is estimated based on the usage of printing at 100 mm/s for 24 hours per day. It may vary depending on the testing conditions and product iteration, and is for reference only.
[4] The data may vary depending on the testing conditions and product iteration, and is for reference only.