Breaking Point: How Strong Are 3D-Printed Parts?
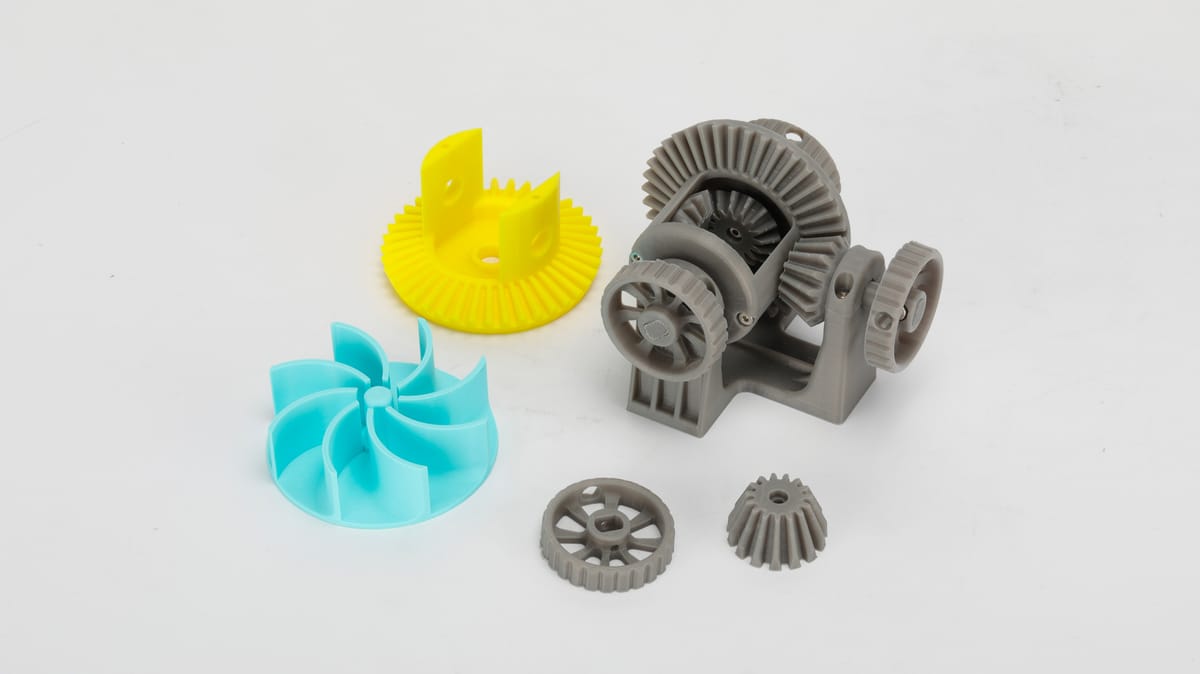
Did you know that some 3D-printed parts can be stronger than 6061 aluminum? The actual strength of 3D-printed parts depends on several factors that affect their performance in real-life applications. Many people think 3D-printed plastic isn't durable. Yet, materials like Polycarbonate pack an impressive tensile strength of about 9800 psi, which makes it the strongest 3D printing material available today.
Your choice of material and printing settings makes a significant difference in the strength of your 3D-printed parts. PLA provides approximately 50 MPa (7250 psi) of tensile strength, but specialized materials like Nylon PA 12 Carbon-filled can achieve up to 76 MPa (11000 psi). Stainless Steel 17.4 takes it even further with an impressive 155,000 psi, making it perfect for aerospace uses. Your part's strength doesn't just depend on the material, though. Factors such as infill density (aim for 50-70% for functional parts), infill pattern, layer height, and post-processing methods all play a role. The annealing process can boost strength by about 40% by reorganizing the material's internal structure.
This piece will show you the real breaking points of 3D-printed components. We'll examine various materials, optimal print settings, and post-processing techniques that can transform delicate plastic parts into reliable, functional components suitable for critical industries.
Common 3D Printing Materials and Their Strength Profiles
The right material choice builds the foundation of 3D print strength. Different filaments have unique mechanical properties that make them perfect for specific uses.
PLA: 50 MPa Tensile Strength with Brittle Failure
PLA is one of the most versatile 3D printing materials, with an impressive tensile strength of 53-59 MPa. While it's strong, PLA breaks easily, which means it's not great for things that need to resist impact. The material remains rigid and strong but starts to soften at around 52°C, so it is not suitable for use in high-temperature environments. Studies show that PLA's tensile strength varies depending on the printing method and raster angle. The strength usually goes up as the raster angle shifts from 0° to 90°.
ABS: High Impact Resistance and Flexural Strength
ABS gives you amazing toughness with impact strength between 12 kJ/m² and 30 kJ/m². Its tensile strength is lower than PLA at 34-36 MPa, but ABS makes up for this with better impact resistance and heat tolerance up to 98°C. The material's flexural strength reaches 60-61 MPa, making it ideal for applications that require high-stress resistance. These qualities make ABS a great choice for car parts, consumer electronics, and protective gear where you need good impact resistance.
PETG: Balanced Strength and Flexibility
PETG sits right between PLA's rigidity and ABS's toughness. With a tensile strength of 38-44 MPa and flexural strength of 75-79 MPa, PETG has great layer adhesion and resists bending forces well. Impact tests show that PETG has XY impact resistance between 7-14 kJ/m², which beats both PLA and ABS in some uses. It also stays stable up to 73°C, handling heat better than PLA while being easier to print than ABS.
Polycarbonate: Strongest 3D Printing Material for Impact Loads
Polycarbonate stands out as the clear winner among common 3D printing materials, with tensile strength reaching 9,800 psi (about 72 MPa). Tests show that this is a significant issue, as it means that PC can lift 685 pounds, which is significantly above PLA's 285-pound limit. Polycarbonate also has very high heat resistance with a glass transition temperature of 150°C, so it keeps its shape even in tough heat conditions. These features make polycarbonate the best choice for engineering projects that just need exceptional strength and durability.
Print Settings That Directly Affect 3D Print Strength
Print settings play a huge role in making 3D-printed objects stronger, just like material choice does. Smart adjustments to these settings can turn regular filaments into really strong parts.
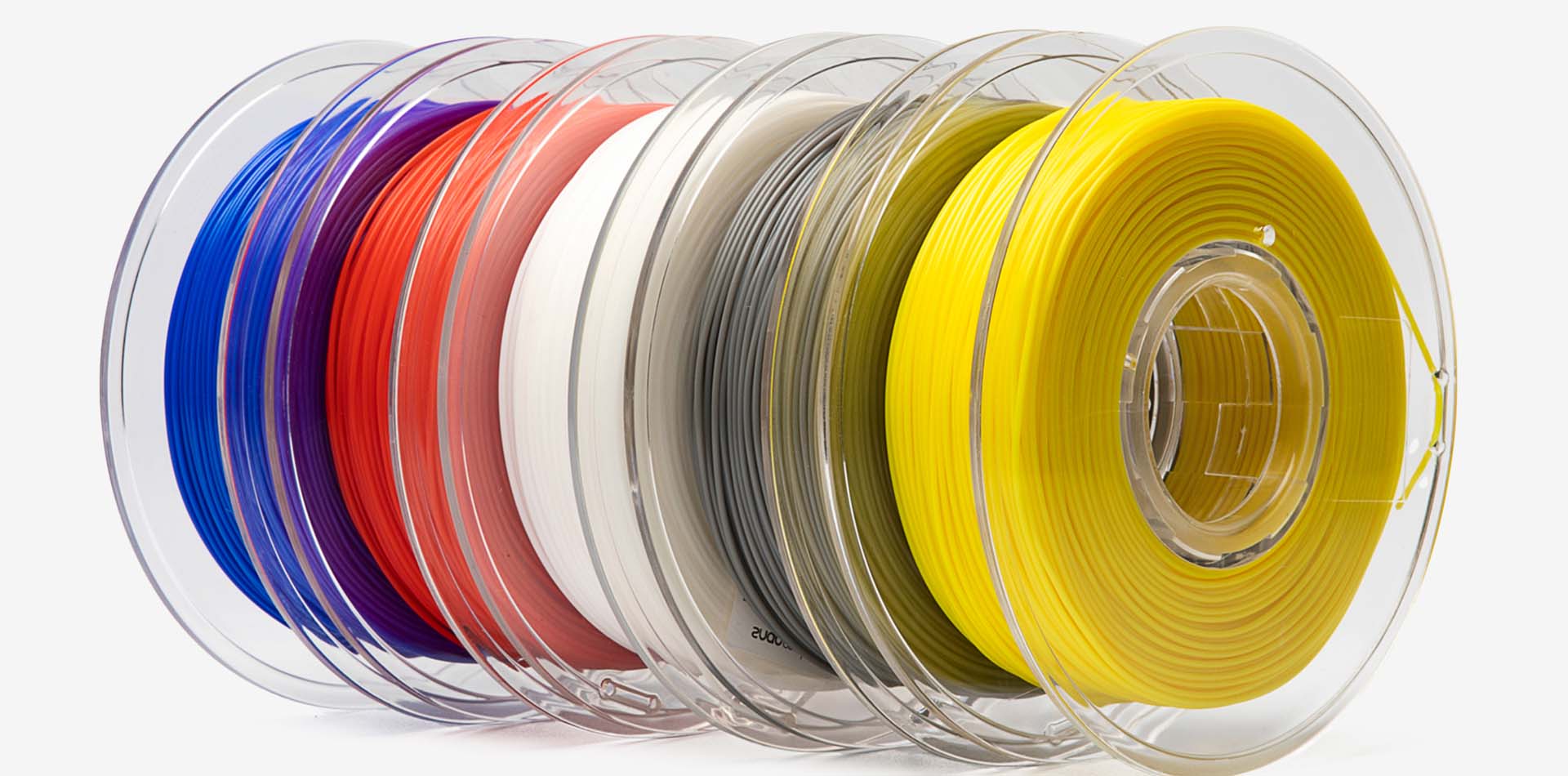
Optimal Printing Temperature for Layer Adhesion
Temperature plays a key role in how well layers stick together. Research indicates that printing at higher temperatures within the recommended range enhances the bonding of layers. PLA printed at 210°C shows 39 MPa strength, compared to just 37 MPa at 200°C. PETG reaches 60% of its full strength at 245°C, but only 33% at 200°C. You'll get the strongest prints by setting temperatures close to your filament's upper limit.
Layer Height vs. Line Width: Strength Trade-offs
Layer height and line width each affect part strength differently. Parts become weaker when layer heights go above half the nozzle diameter (0.2mm for a 0.4mm nozzle). Line width tells a different story - pushing it up to 150% of nozzle diameter creates better layer bonding through increased pressure. The strongest parts come from thin layers (0.1-0.2mm) paired with wider extrusion lines (120-140% of nozzle diameter).
Infill Pattern and Density: Honeycomb vs. Grid
The sweet spot for infill density lies between 50% and 70%, as going higher doesn't add much strength. Triangle patterns stand out for strength because they resist warping better. Honeycomb patterns give you the best strength-to-weight ratio but take longer to print. Grid patterns work best when you need 100% infill for maximum strength.
Wall Thickness: Recommended 2–3 mm for Load-Bearing Parts
Wall thickness matters more than infill for functional parts. Load-bearing pieces need 4-6mm shell thickness, while regular parts work fine with 1.6mm (2-4 perimeters). Thicker walls help spread out stress and stop big gaps from forming inside.
Part Orientation: Maximizing Strength in X-Y vs. Z Axis
3D-printed parts are 4-5 times stronger in the XY-plane than in the Z-axis. This happens because layers tend to separate at their meeting points. Parts work best when tension forces line up with layers and compression forces cross them. Brackets and load-bearing parts should avoid forces that pull across layer lines.
How 3D-Printed Parts Compare to Traditional Manufacturing
Traditional manufacturing methods and 3D printing take completely different paths to create parts. Each approach has its own strength profile that makes it right for different uses.
Injection Molding vs. 3D Printing: Layer Adhesion vs. Homogeneity
Parts made through injection molding are stronger than their 3D-printed counterparts because of their uniform structure. The layer-by-layer approach of 3D printing differs from injection molding's solid, uniform parts that have consistent mechanical properties. This key difference leads to anisotropy - 3D-printed parts show the most strength along the horizontal plane but become weakest between layers, where they often split apart. The strength of injection molded parts remains the same in all directions.
When 3D Printing is Strong Enough for End-Use Applications
Though traditional manufacturing wins on strength, 3D printing keeps finding its place in real-world uses. Aerospace companies utilize 3D-printed parts to reduce weight while maintaining sufficient strength, thereby streamlining their processes. Car makers also use 3D printing to make complex transmission parts and lightweight structures.
New materials like carbon-fiber-reinforced filaments and metal printing have helped close the strength gap. Special finishing techniques, such as annealing, help 3D-printed parts match those made by injection molding in certain applications. The unique way 3D printing creates complex internal structures at no extra cost lets designers make things that traditional manufacturing never could. Sometimes, this clever geometry makes up for any strength limitations.
The Final Thought
Our in-depth examination of 3D-printed components reveals that their strength stems from multiple interconnected factors, not just material selection. Material selection is a vital starting point. Polycarbonate leads with 9,800 psi tensile strength, and carbon-filled nylons challenge these limits even more.
Print settings are just as significant. The right temperature settings boost layer adhesion. A perfect mix of layer height and line width improves structural integrity by a lot. Additionally, strategic infill patterns, such as triangular and honeycomb, offer remarkable strength-to-weight ratios at densities of 50-70%.
Post-processing methods turn basic prints into industrial-grade parts. To cite an instance, annealing reorganizes molecular structures and delivers up to 40% strength improvements. Carbon or glass fiber reinforcement creates parts that match aluminum's strength in some uses. Traditional parts still outperform 3D prints in raw strength, but this gap is narrowing.
The real question about strength becomes: "Strong enough for what purpose?" Many functional applications in the aerospace, automotive, and consumer goods sectors demonstrate that optimized 3D-printed parts meet or exceed the required standards. These parts aren't just strong enough - they offer design freedom that makes complex shapes possible, unlike traditional manufacturing.
3D-printed parts might never match the isotropic properties of injection-molded components. However, their customizable strength profiles and geometric optimization make them viable alternatives. The future looks bright as materials science and printing technologies advance, expanding what this game-changing manufacturing approach can do.